How to Calculate and Formula for Cost of Production: The Key to Your Business Success
May 15, 2024
Share This Article
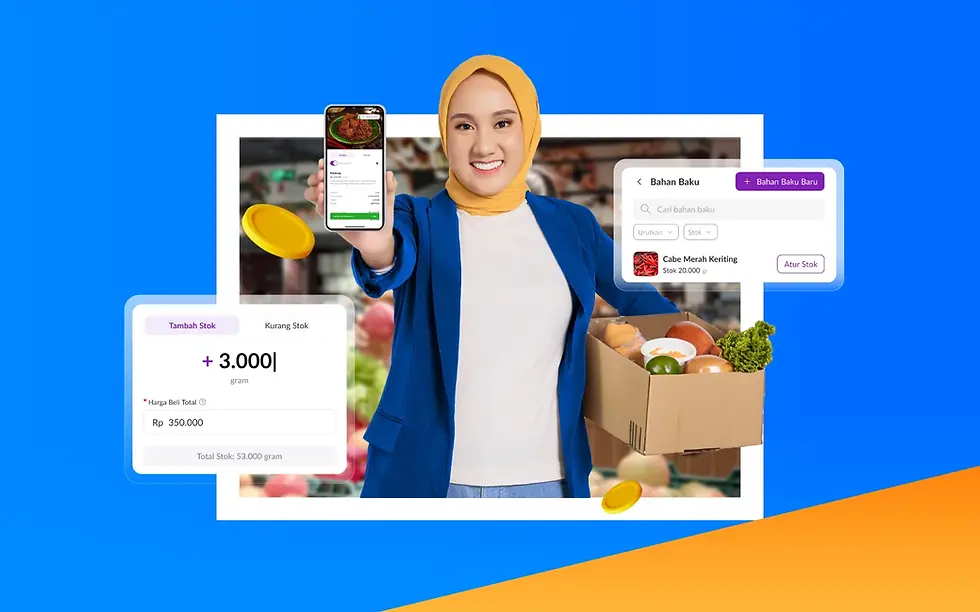
In the ever-evolving world of business, mastering the cost of production formula is like having a compass that always points north.
For you, the brave UMKM warriors and entrepreneurial adventurers, understanding these details isn’t just about numbers—it’s about navigating your business toward the peak of success.
Let’s embark on this journey together, sailing through the vast ocean of business with the most valuable map: knowledge of the cost of production.
Definition of Cost of Goods Manufactured (COGM)
COGM (Cost of Goods Manufactured) is the total cost incurred to produce goods or services that are ready for sale. It’s not just about the money spent on raw materials but also about how energy, time, and other resources come together to create something valuable.
In the dynamic world of business, the cost of goods manufactured is like a canvas on which you paint your strategies and innovations.
3 Key Components of the Cost of Goods Manufactured (COGM)
Raw materials, direct labor, and factory overhead are more than just numbers in a financial report—they are the key metrics that bring your product to life.
Let’s dive deeper into these three components and understand why they are inseparable in building your business empire.
1. Raw Materials
Raw materials are the heart of every creation—the shining star of your production process. Just like a seed that grows into a lush tree, raw materials form the foundation of every product you offer.
However, remember that the quality of the seed determines the quality of the tree. Similarly, the quality of raw materials directly impacts the final product.
When selecting raw materials, consider sustainable and ethical sourcing. It’s not just about creating high-quality products, but also about building a positive brand image in the eyes of your customers.
2. Direct Labor
Next, there is direct labor—the artisans whose hard work often remains unseen behind the brilliance of the final product. They are the hands that carve, paint, and assemble, breathing life into raw materials.
In this era of automation, don’t overlook the human touch that can add unique value to your products. Investing in their well-being and skill development will not only enhance product quality but also foster loyalty and boost productivity.
3. Factory Overhead
Factory overhead is the unseen director behind the scenes, orchestrating every element of production to ensure that the show must go on. From the electricity that powers the factory lights to the maintenance of machines that keep production running smoothly, factory overhead consists of costs that often go unnoticed but are vital to operations.
Managing overhead requires intelligence and innovation. For instance, adopting renewable energy sources or automating processes can significantly reduce these costs.
Aligning these three components to create harmony in production is no easy task. However, with the right strategy, you can compose a captivating symphony.
For example, leveraging the latest technology can optimize raw material usage and improve labor efficiency. Meanwhile, effective waste management practices can help lower factory overhead while also contributing to environmental sustainability.
Also Read: Pricing Strategy: Definition, Factors, and 25 Types
Formula for Cost of Goods Manufactured (COGM)
After understanding the importance of the Cost of Goods Manufactured (COGM) in business, let's dive deeper into this concept.
In today’s fast-paced world, mastering the COGM formula is like having a treasure map.
This time, we will explore three essential formulas that can help you become a skilled captain in steering your business ship.
1. Basic Formula for Cost of Goods Manufactured (COGM)
First, there is the basic COGM formula, which serves as the foundation of production cost calculation. The formula is quite simple:
COGM = Raw Material Costs + Direct Labor Costs + Factory Overhead Costs
This formula represents the total cost incurred to manufacture goods. The main objective is, of course, to determine how much it costs to produce a product so that you can set the right selling price.
Example of Calculating the Basic Cost of Goods Manufactured (COGM) Formula:
For instance, if your raw material costs are Rp10,000, direct labor costs are Rp5,000, and factory overhead costs are Rp3,000, then your COGM would be Rp18,000.
2. COGM Formula with Inventory
Next, we have the COGM formula with inventory, which is slightly more complex.
The Formula:
COGM = Beginning Inventory + Purchases - Ending Inventory
This formula is used to calculate production costs while considering the stock you have. The goal is to get a more accurate picture of production costs by factoring in existing inventory.
Example of Calculating COGM with Inventory:
For example, if your beginning inventory is Rp5,000, purchases during the period amount to Rp20,000, and your ending inventory is Rp4,000, then your COGM would be Rp21,000.
3. Activity-Based Costing (ABC) Method
Lastly, there is the Activity-Based Costing (ABC) method, which is like dancing with numbers. ABC is a method that allocates overhead costs to products and services based on the activities that incur those costs.
The formula may vary, but the basic concept is:
HPP = Raw Material Costs + Direct Labor Costs + (Overhead Costs per Activity × Number of Activities)
The ABC method aims to provide a more accurate picture of production costs. It allows businesses to better assess the costs associated with each component of production, leading to more precise pricing and cost management.
Example of Calculating the Cost of Goods Manufactured Using the Activity-Based Costing (ABC) Method:
For example, if your raw material cost is Rp10,000, direct labor cost is Rp5,000, overhead cost per activity is Rp2,000, and the number of activities is 3, then the HPP using the ABC method would be Rp16,000.
Also Read: Production Cost Calculation: Definition, Benefits, Cost Components, and How to Calculate It
Cost of Production vs. Total Production Cost
The cost of production and total production cost are two distinct calculations, but both are equally important. Let's make this navigation easier with a comparison table and a real-world example to better understand these concepts.
How to Calculate the Basic Production Cost and Total Production Cost
Imagine you have a growing cookie business. For a 350-gram box of cookies, let's calculate the Cost of Production (HPP) and the Total Production Cost:
Raw Material Costs:
Flour: Rp2,000
Sugar: Rp1,500
Eggs: Rp2,000
Other ingredients (butter, chocolate, etc.): Rp3,000
Total Raw Material Cost: Rp8,500
Direct Labor Cost:
Worker wages: Rp1,500
Direct Production Overhead Costs:
Electricity: Rp500
Equipment depreciation: Rp500
Total Production Overhead Costs: Rp1,000
Cost of Goods Manufactured (COGM) per Box:
COGM = Raw Material Costs + Direct Labor Costs + Production Overhead Costs
COGM = Rp8,500 + Rp1,500 + Rp1,000 = Rp11,000
Total Production Cost:
Administrative Costs: Rp1,000
Marketing Costs: Rp1,500
Total Production Cost per Box:
Total Production Cost = COGM + Administrative Costs + Marketing Costs
Total Production Cost = Rp11,000 + Rp1,000 + Rp1,500 = Rp13,500
Understanding the basic production cost formula is just the first step in a long journey toward business success. No matter how far you go, Labamu is always ready to be your trusted companion.
With the "Manage Raw Materials" feature, Labamu helps you meticulously track and manage every component of your cost of goods manufactured (COGM), ensuring precision and efficiency in every step of your business
.
Visit our page at Labamu and be part of the digital revolution by downloading the Labamu app. Enjoy a free Premium trial to unlock seamless operations, efficiency, and business growth.
With Labamu, every detail of your production cost formula becomes your strength in achieving your dreams. Join us on this journey and turn every challenge into an opportunity with Labamu.